Nonferrous
refers to metals that do not contain significant amounts of iron. These metals are distinguished from ferrous metals, which are primarily composed of iron. Nonferrous metals have different properties and uses compared to ferrous metals, and they are often valued for their resistance to corrosion, electrical conductivity, and lightweight properties. Some common nonferrous metals include: Copper, Nickel, Zinc Lead etc.

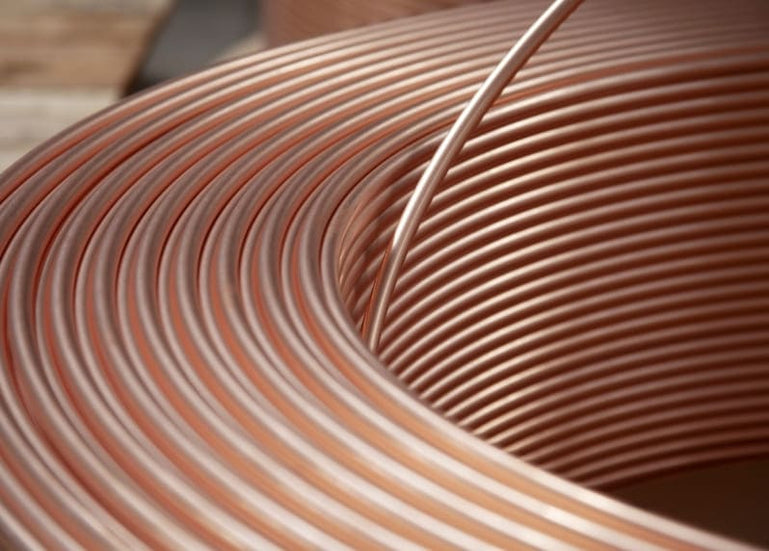
It typically contains various minerals and compounds besides copper, such as sulfur (in the form of copper sulfides like chalcopyrite), iron, and other trace elements. It occurs in different forms, including oxides, carbonates, sulfides, and native copper (copper in its metallic form). Depending on the mineralogy, copper ore can range in color from greenish-blue (chalcopyrite) to reddish-brown (cuprite) and black (tennantite).
Copper ore is extracted from open-pit or underground mines using mining techniques such as drilling, blasting, and hauling. After mining, copper ore undergoes several stages of processing, including crushing and grinding to liberate the valuable minerals, followed by froth flotation to concentrate the copper minerals into a saleable product.
The primary use of copper ore is in metallurgical processes, where it is smelted to produce copper metal for various applications, including electrical wiring, plumbing, and industrial machinery. During processing, copper ore may also yield valuable by-products such as gold, silver, and molybdenum.

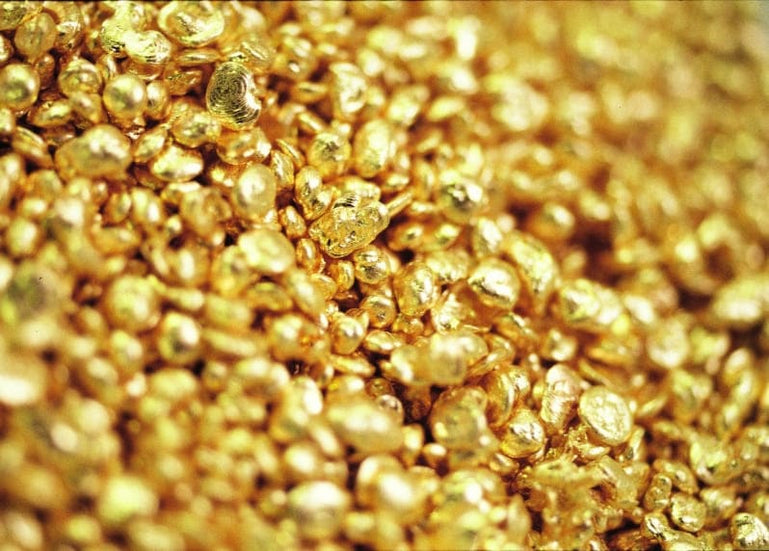
It may contain various minerals such as quartz, pyrite, and sulfides alongside native gold or gold-bearing minerals like gold tellurides. It occurs in various forms, including free-milling ores (gold particles easily liberated by grinding), refractory ores (gold locked in sulfides or other minerals), and placer deposits (gold grains in sedimentary deposits).
Gold ore is extracted from underground or open-pit mines using various mining techniques such as drilling, blasting, and extraction methods specific to the ore type. After mining, gold ore undergoes several stages of processing, including crushing, grinding, gravity separation, flotation, and cyanidation (for refractory ores) to extract gold and produce a gold-rich concentrate.
The primary use of gold ore is in metallurgical processes, where it is smelted to produce gold bullion for various applications, including jewelry, electronics, and investment.

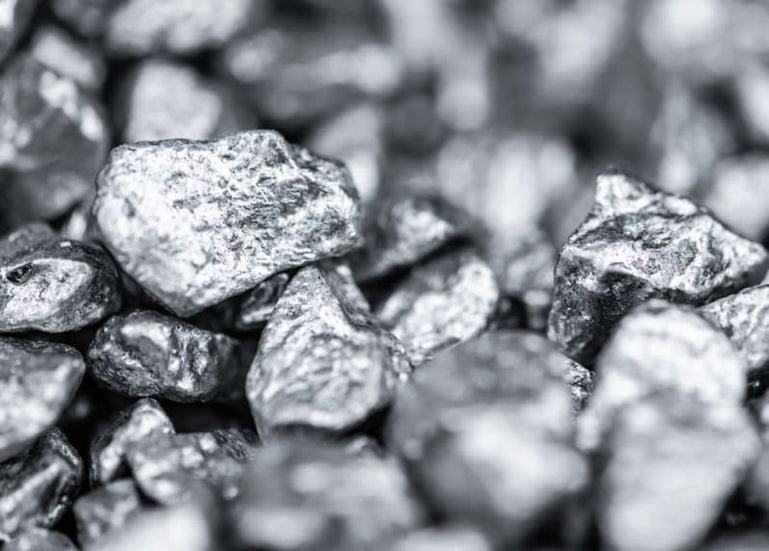
It contains varying amounts of silver, along with other minerals such as quartz, sulfides (like galena and argentite), and sometimes gold. It occurs in various forms, including native silver (pure silver in its natural metallic form), sulfide ores (silver combined with sulfur), and complex ores containing multiple minerals.
Silver ore is typically extracted from underground or open-pit mines using methods similar to those used for other metal ores, such as drilling, blasting, and crushing. After mining, silver ore undergoes processes such as grinding, flotation, and leaching (with cyanide or other chemicals) to separate and concentrate the silver-bearing minerals.
It is primarily used in metallurgical processes to produce silver metal. It is also used in the production of jewelry, silverware, electronics, and photographic materials.

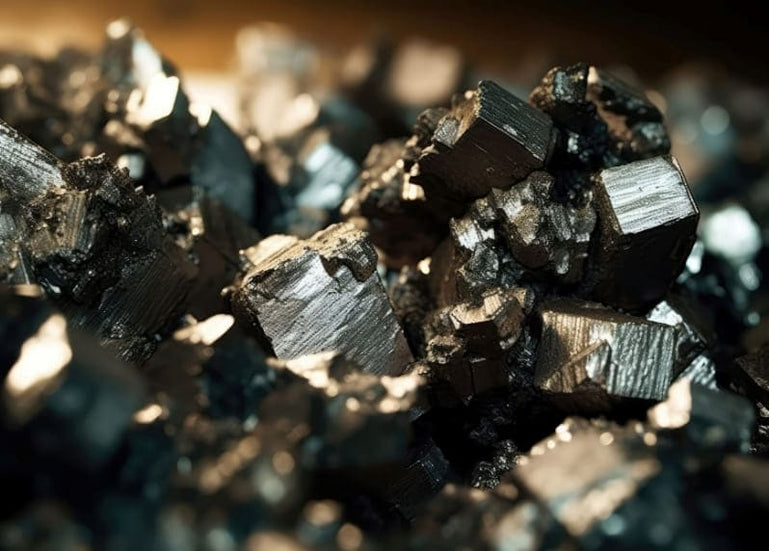
It contains varying amounts of nickel, alongside other minerals such as iron, sulfur, and sometimes cobalt and copper. It occurs in different forms, including sulfide ores (such as pentlandite and pyrrhotite) and laterite ores (formed by weathering of ultramafic rocks).
Nickel ore is typically extracted from open-pit or underground mines using methods like drilling, blasting, and crushing. After mining, nickel ore undergoes processes such as flotation, magnetic separation, and smelting to extract and concentrate nickel-bearing minerals.
It is primarily used in metallurgical processes to produce nickel metal. It is also used in the production of stainless steel, alloys, batteries, and industrial equipment.

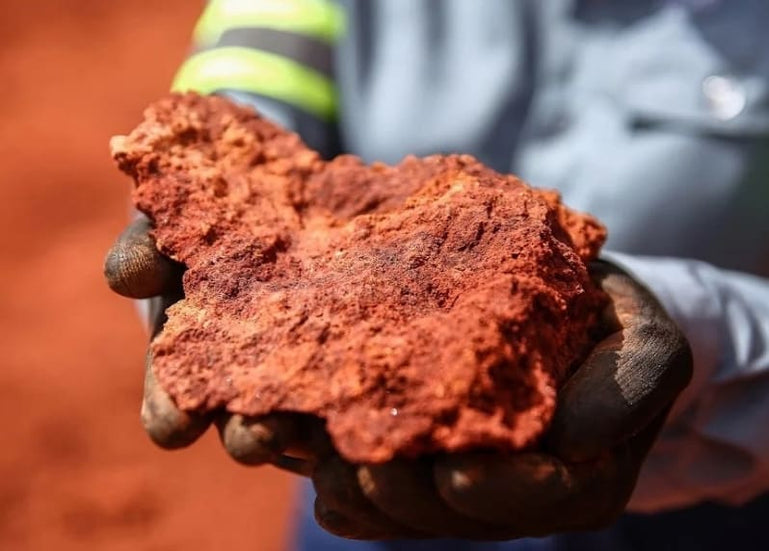
It typically consists of various aluminum hydroxide minerals, along with iron oxides, silica, and other impurities. It ranges in color from reddish-brown to white, depending on the iron content and other mineral impurities. Bauxite forms through weathering and leaching of aluminum-rich rocks in tropical and subtropical regions, often under high rainfall conditions.
Bauxite is extracted from open-pit mines using heavy machinery and explosives. After mining, bauxite undergoes beneficiation processes such as washing, crushing, and refining to remove impurities and concentrate the aluminum content.
The primary use of bauxite is in the production of aluminum metal through the Bayer process, where bauxite is refined into alumina (aluminum oxide), which is then smelted to produce pure aluminum metal. Bauxite is also used in the production of refractories, abrasives, proppants for hydraulic fracturing, and as a raw material in the manufacture of ceramics and chemicals.
Major bauxite-producing countries include Australia, Guinea, China, Brazil, and India. Bauxite is a crucial natural resource for the aluminum industry, providing the primary source of aluminum globally due to its abundance and extractability.

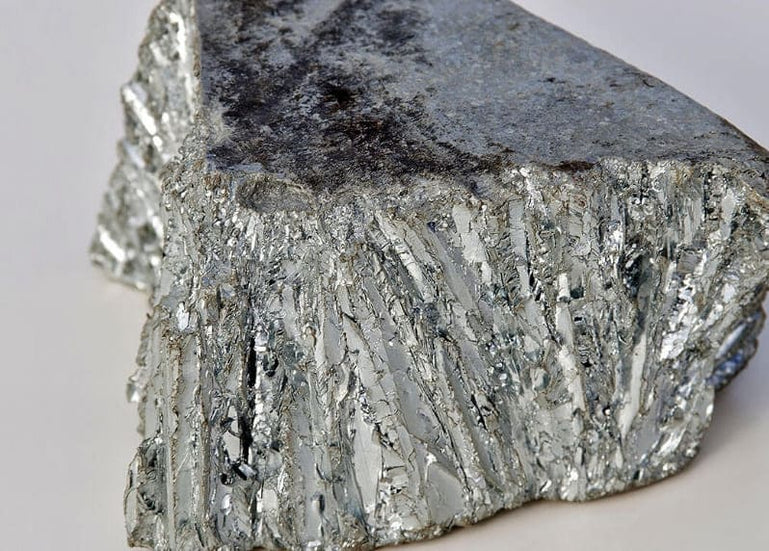
Ferroalloys
are alloys of iron with a high proportion of one or more other elements such as manganese, silicon, chromium, or titanium. These alloys are primarily used in the production of steel and cast iron, as they serve to impart specific properties to the metal. They are produced by smelting mixed ores and other materials in a submerged electric arc furnace or blast furnace. They play a crucial role in modern metallurgy, enhancing the quality and properties of steel and iron, making them suitable for a wide range of industrial applications.

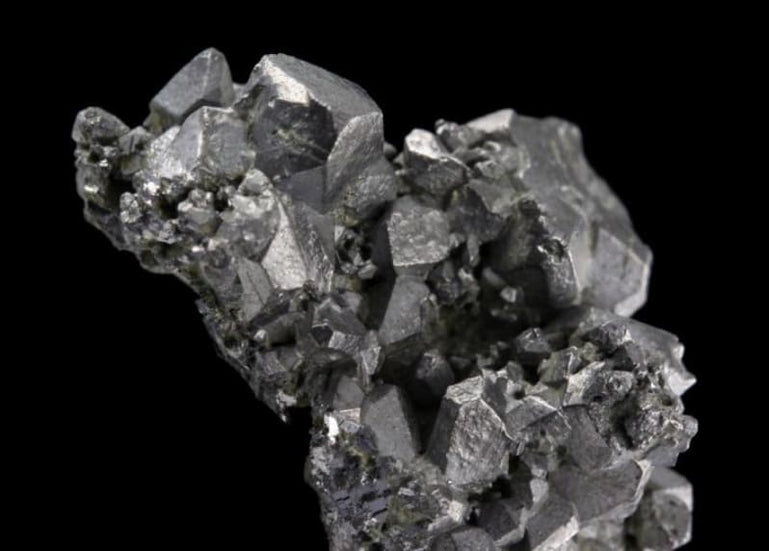

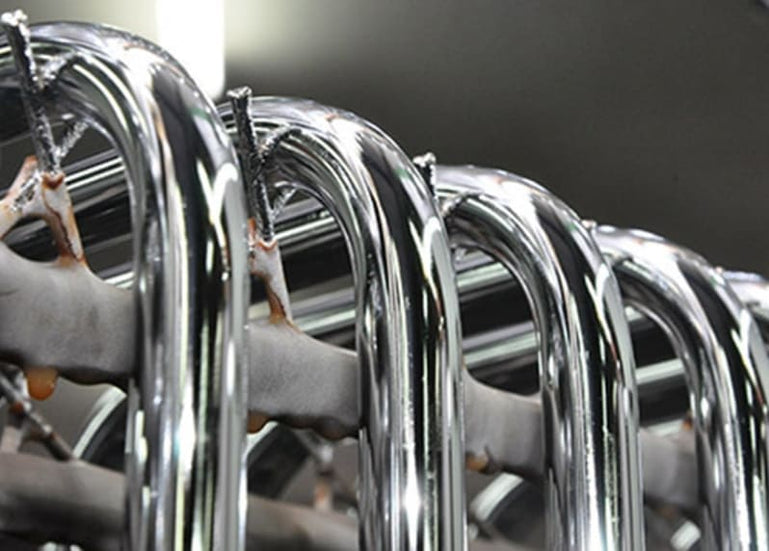
Chrome ore is a natural mineral resource from which chromium, a metallic element, is extracted. The most common form of chrome ore is chromite (FeCr₂O₄), which contains chromium, iron, and oxygen. Chromite is typically found in layered igneous rock formations known as chromitite seams. The extraction process involves mining, crushing, and grinding the ore, followed by concentration techniques such as gravity separation or flotation to produce a concentrated form of chromite.
Chromium extracted from chrome ore is essential for the production of various materials, including:
- Stainless Steel: Chromium enhances the corrosion resistance and hardness of steel.
- Refractory Material: Used in high-temperature applications due to chromium's ability to withstand extreme conditions.
- Chemical Production: Chromium compounds are used in dyes, pigments, and electroplating.
The unique properties of chromium make chrome ore a valuable resource in industrial manufacturing and metallurgy.

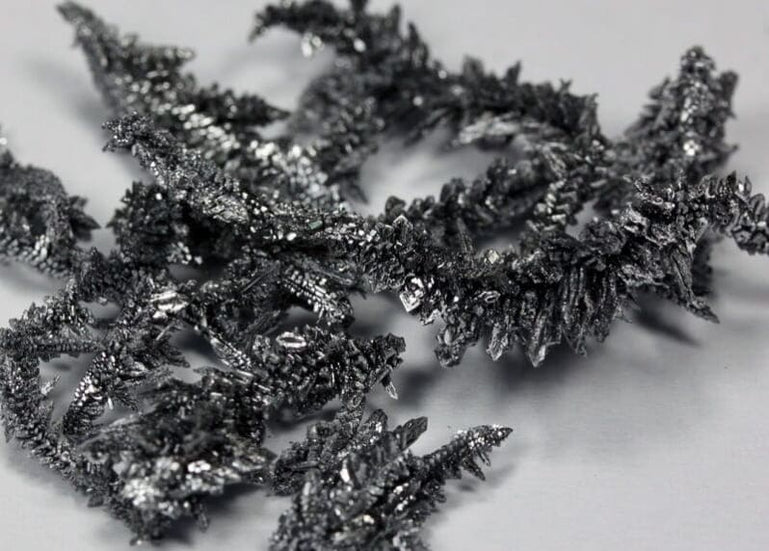
The extraction process involves mining, crushing, and milling the ore, followed by concentration techniques such as flotation, gravity separation, or magnetic separation to isolate the vanadium-bearing minerals. The concentrated ore is then subjected to roasting and leaching to produce vanadium pentoxide (V₂O₅), which can be further processed to produce various vanadium products.
Vanadium has several industrial applications, including:
- Steel Production: Vanadium is used as an alloying element to improve the strength, toughness, and wear resistance of steel.
- Aerospace: Vanadium alloys are used in the aerospace industry for their high strength-to-weight ratio and resistance to heat and corrosion.
- Energy Storage: Vanadium redox flow batteries (VRFBs) are used for large-scale energy storage applications due to their long cycle life and scalability.
- Chemical Industry: Vanadium compounds are used as catalysts in the production of sulfuric acid and other chemicals.